Przeciętny pracownik poświęca 17 minut dziennie na zgłaszanie awarii i przyczyn przestoju.
U NAS LICZY SIĘ
PRODUKCJA
Jedyne narzędzie którego potrzebujesz, aby zarządzać produkcją w czasie rzeczywistym
Jedyne narzędzie którego potrzebujesz,
aby zarządzać produkcją w czasie rzeczywistym
CZY WIESZ, ŻE
Przeciętny pracownik produkcji ponad 20% czasu spędza na czynnościach nieprzynoszących wartości
Na co tracisz czas w swoim zakładzie?
Roczny koszt nieefektywności pracowników to, w przypadku firmy zatrudniającej 500 osób, ponad
4 000 000 zł
Zależy Ci na Twojej produkcji?
Zacznij się jej przyglądać!
Problemy, z którymi mierzą się pracownicy produkcji nie są nam obce. Nasze spojrzenie na produkcję łączy różne perspektywy, dając spójny i całościowy obraz. Dzięki niemu potrafimy dostrzec jak wygląda cały proces i skupić się na przepływie, a nie tylko pojedynczych elementach.
Zależy Ci na Twojej produkcji?
Zacznij się jej przyglądać!
Problemy, z którymi mierzą się pracownicy produkcji nie są nam obce. Nasze spojrzenie na produkcję łączy różne perspektywy, dając spójny i całościowy obraz. Dzięki niemu potrafimy dostrzec jak wygląda cały proces i skupić się na przepływie, a nie tylko pojedynczych elementach.
W CZASIE RZECZYWISTYM
Z Kanri monitorujesz produkcję na bieżąco.
Nie czekasz na wypełnienie przez pracowników tabelek i dostarczenie raportu – reagujesz wtedy, gdy występują problemy.
BEZ MARNOTRAWSTWA
Ręczne raportowanie zdarzeń na produkcji jest czasochłonne i bezproduktywne.
Dzięki Kanri dane zbierane są automatycznie z Twoich maszyn lub poprzez jedno kliknięcie Twojego pracownika.
PROSTO Z PRODUKCJI
Nasze urządzenia zbierają dane bezpośrednio z maszyn i od ich operatorów.
Tak gromadzone informacje nie są obarczone błędem ludzkim – pokazują faktyczny stan Twoich procesów i wszelkie występujące zaburzenia.
W CZYTELNEJ FORMIE
Kanri to koniec z wypełnianiem tabelek, zliczaniem i podsumowywaniem wyników.
Teraz wszystkie dane masz dostępne w jednym miejscu, w formie czytelnych wykresów i alertów o nieprawidłowościach.
Z NACISKIEM NA PROCES
Kanri, pokazując przepływ w całym procesie, pomaga identyfikować wąskie gardła i przyczyny nieefektywności nie na pojedynczych stanowiskach, ale w całym toku produkcji, dzięki czemu walczy ze zjawiskiem silosów w organizacji.
Zależy Ci na Twojej produkcji?
Zacznij się jej przyglądać!
Problemy, z którymi mierzą się pracownicy produkcji nie są nam obce. Nasze spojrzenie na produkcję łączy różne perspektywy, dając spójny i całościowy obraz. Dzięki niemu potrafimy dostrzec jak wygląda cały proces i skupić się na przepływie, a nie tylko pojedynczych elementach.
W CZASIE RZECZYWISTYM
Z Kanri monitorujesz produkcję na bieżąco. Nie czekasz na wypełnienie przez pracowników tabelek i dostarczenie raportu – reagujesz wtedy, gdy występują problemy.
BEZ MARNOTRAWSTWA
Ręczne raportowanie zdarzeń na produkcji jest czasochłonne i bezproduktywne. Dzięki Kanri dane zbierane są automatycznie z Twoich maszyn lub poprzez jedno kliknięcie Twojego pracownika.
PROSTO Z PRODUKCJI
Nasze urządzenia zbierają dane bezpośrednio z maszyn i od ich operatorów. Tak gromadzone informacje nie są obarczone błędem ludzkim – pokazują faktyczny stan Twoich procesów i wszelkie występujące zaburzenia.
W CZYTELNEJ FORMIE
Kanri to koniec z wypełnianiem tabelek, zliczaniem i podsumowywaniem wyników. Teraz wszystkie dane masz dostępne w jednym miejscu, w formie czytelnych wykresów i alertów o nieprawidłowościach.
Z NACISKIEM NA PROCES
Kanri, pokazując przepływ w całym procesie, pomaga identyfikować wąskie gardła i przyczyny nieefektywności nie na pojedynczych stanowiskach, ale w całym toku produkcji, dzięki czemu walczy ze zjawiskiem silosów w organizacji.
Wizja nowoczesnej produkcji w zasięgu ręki
Sprawdź jak Kanri może pomóc w optymalizacji Twojej pracy
Sercem Kanri jest produkcja. Łączymy wiedzę i pasję z doświadczeniami naszych Klientów, wspólnie udoskonalając procesy produkcyjne już od
4 lat
Sprawiamy, że procesy produkcyjne stają się czytelne i zrozumiałe
Kanri to narzędzie do kompleksowego zarządzania produkcją. Dzięki dedykowanym panelom pracownicy mogą z łatwością raportować swoją pracę i wszelkie nieprawidłowości, a kierownicy – podejmować decyzje, planować działania i delegować obowiązki.
ZAUFALI NAM
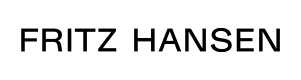
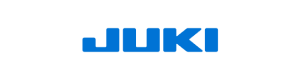
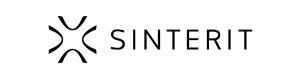
Nasze realizacje
Zobacz, jak przebiega wdrażanie KanriSoft w praktyce.
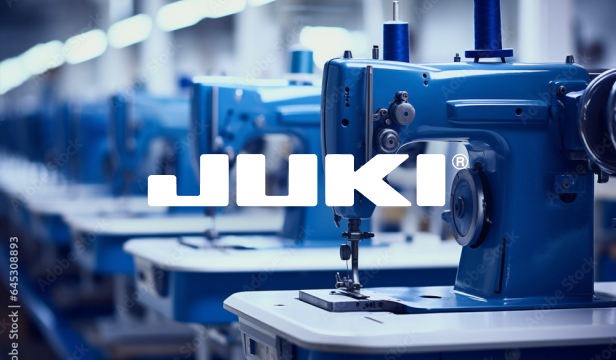
BRANŻA
Jakiś Chwytliwy Tytuł
Officia provident autem assumenda quia cumque voluptas voluptatibus. Minus aliquid est quas modi est ab unde enim. Molestiae eius eveniet vero dolor nihil quasi doloribus nulla.
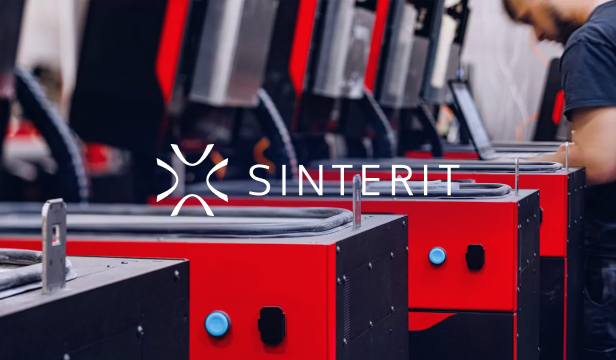
BRANŻA
Jakiś Chwytliwy Tytuł
Officia provident autem assumenda quia cumque voluptas voluptatibus. Minus aliquid est quas modi est ab unde enim. Molestiae eius eveniet vero dolor nihil quasi doloribus nulla.
Co mówią o Kanri
Dowiedz się, za co doceniają Kanri nasi dotychczasowi Klienci.
Co mówią o Kanri
Dowiedz się, za co doceniają Kanri nasi dotychczasowi Klienci.
Najczęściej zadawane pytania
Poznaj odpowiedzi na najczęściej zadawane pytania dotyczące Kanri
Techniczne właściwości Kanri
W jaki sposób Kanri łączy się z maszynami?
Kanri łączy się z Twoimi maszynami dzięki wykorzystaniu autorskiego rozwiązania IoT, poprzez połączenie cyfrowe (24 VDC) lub analogowe (4-20 mA, 0-10V).
Jaki sprzęt (gniazdka, kable itp.) jest niezbędny do podłączenia?
Do podłączenia niezbędne jest zasilanie 230V, podłączenie do sieci kablem ethernet, tablet jako HMI, a także dodatkowe peryferia takie jak przyciski czy bramki (tam gdzie ma to uzasadnione wykorzystanie).
Jakie są wymagania dla infrastruktury sieciowej?
Kanri wymaga podłączenia do sieci kablem ethernet. Zalecamy wydzielenie odrębnej podsieci, choć nie jest to niezbędne. Wsparcie techniczne realizujemy zdalnie za pomocą tuneli VPN, w przypadku braku możliwości utrzymania stałego połączenia VPN, Kanri dostarczane jest wraz z pełnym pakietem monitoringu umożliwiającym lokalnemu IT monitorowanie stanu systemu.
Czy Kanri jest rozwiązaniem chmurowym?
Tak, Kanri jest rozwiązaniem w chmurze MS Azure, może być też zainstalowane w niemal dowolnej innej chmurze publicznej (np. AWS, GCP), prywatnej (OpenStack, ProxMox itp), zainstalowane na serwerze on premise bądź w wersji hybrydowej łączącej zasoby chmury i lokalne.
Jak wyglądają kwestie zgodności (compliance) z regulacjami wewnątrz firmy?
Każdorazowo podczas wdrożenia analizowane są wymagania compliance z Twoim działem IT i polityką cybersecurity Twojego zakładu.
Czy Kanri jest zgodne z obowiązującymi normami RODO, ISO itp.?
Kanri jest częścią CSHARK, który funkcjonuje zgodnie z ISO 9001. Zgodność z RODO zapewnia także chmura MS Azure, dane klientów przechowywane są w oddzielnych bazach danych, wyłącznie na terytorium UE.
Integracja z istniejącymi systemami
Czy Kanri może się integrować z innym oprogramowaniem (ERP, WMS, APS itp.)?
Tak, Kanri może integrować się z zewnętrznymi systemami poprzez API lub dedykowane aplikacje middleware tworzone w procesie wdrażania przez zespół programistów CSHARK/Kanri pod konkretne potrzeby. Z założenia Kanri ma stworzyć jeden spójny interfejs do współpracy z systemami ERP, WMS, APS, etc.
Czy Kanri może się integrować z systemami tworzonymi wewnętrznie?
Tak, o ile są zaprojektowane w sposób który to umożliwia. Możliwości integracji badane są przez zespół analityków Kanri podczas wdrożenia lub analizy przedwdrożeniowej.
Wdrożenie Kanri
Ile trwa wdrożenie Kanri?
Wdrożenie Kanri zaczyna się od wizji lokalnej w Twoim zakładzie, sesji workshopów mapujących i definiujących zakres wdrożenia oraz procesu instalacji i uruchomienia Kanri w Twoim zakładzie. Całość trwa od kilku tygodni do kilku miesięcy.
Sama fizyczna instalacja urządzeń IoT jest bardzo prosta i może zostać wykonana także przez lokalny dział utrzymania ruchu na podstawie dostarczonej dokumentacji
Jakie dodatkowe akcesoria muszę kupić w celu wdrożenia Kanri?
Tablet jako HMI dla operatorów maszyn, okablowanie, serwer lokalny dla instalacji on premise, dodatkowe elementy typu przyciski, jeśli Twoje maszyny nie umożliwiają integracji z IoT.